A Roadmap to Quality and Cost-Efficiency
In the intricate and highly specialized sector of Class III catheter and implant manufacturing, achieving a synergy between cost-efficiency and quality is a critical goal. As a dedicated Contract Development and Manufacturing Organization (CDMO) for Class III medical devices, our mission is centered around the integration of cost-conscious strategies with the stringent quality demands these life-supporting devices require.
Enhancing Compliance Efficiency
The journey through regulatory compliance for Class III devices is particularly challenging due to their high-risk nature. Our seasoned team leverages an advanced understanding of these rigorous regulatory demands to streamline the compliance process. By preemptively addressing potential compliance issues, we significantly cut down on costly delays and product revisions, thereby delivering cost savings to our clientele without compromising on the requisite high standards.
Precision-Timed Development and Manufacturing
The essence of Class III device manufacturing is precision-timed execution. Delays are not just setbacks; they can be deal-breakers. Our adept project management and manufacturing execution are calibrated to deliver products on schedule, facilitating our clients to hit critical market windows and optimize cost management.
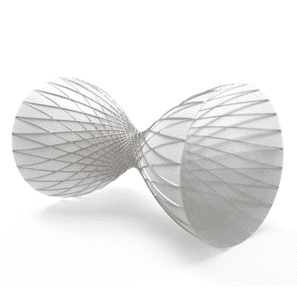
Understanding the critical nature of clinical trials and regulatory approvals, we offer a specialized phase of manufacturing we refer to as Pilot Production. This phase is tailored to support the intricate process of clinical validation, which can span several years. Our willingness to produce small lots of product qualified for clinical use is a testament to our flexibility and commitment to supporting our clients through every stage of product development. Pilot Production allows for the essential gathering of clinical data without the need to invest in full-scale production runs, thereby optimizing resource allocation and cost.
Pilot Production serves as a bridge between the developmental prototypes and the full-scale manufacturing that follows regulatory approval. This pivotal phase provides several benefits: it enables early-stage clinical testing, facilitates iterative design enhancements informed by trial outcomes, and significantly reduces the time to market post-approval.
By providing high-quality, trial-ready products during this critical evaluation stage, we help our clients stay agile and responsive to emergent data, ensuring that when the time comes for mass production, the transition is seamless, swift, and economically sound.
Unyielding Commitment to Quality
In the realm of Class III devices, quality assurance is the cornerstone of manufacturing. Employing state-of-the-art technologies and forward-thinking manufacturing practices, we guarantee each device emerges from production meeting the highest echelons of quality. Our stringent quality control measures are designed to deliver reliability batch after batch, ensuring that our clients can depend on the excellence of our products without incurring the additional costs associated with rework or product recalls.
Transparent and Proactive Communication
Our commitment to transparency cements our partnership with clients. Through consistent and clear communication, we foster an environment of mutual trust and understanding, aligning our manufacturing process with the precise budgetary and product requirements of our clients.
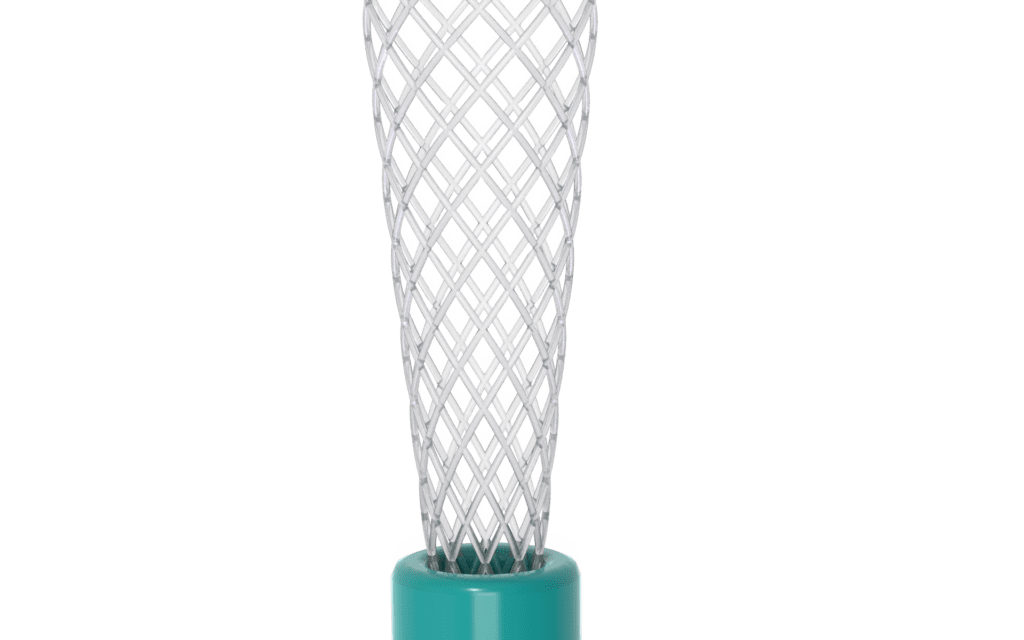
Tailored Solutions, Optimized Costs
Class III medical devices often demand highly specialized solutions. Our approach is to provide bespoke customization that aligns with the specific needs of each project without disproportionately affecting the cost. We achieve this through adaptable manufacturing processes that are as efficient as they are innovative.
In our relentless pursuit of quality, we commonly suggest a strategic investment in process development before the medical device design verification phase. This proactive stance allows us to refine manufacturing processes in tandem with the design itself, rather than retrofitting improvements after design verification.
This approach not only enhances the quality and performance of the product for design verification and clinical trials but also streamlines the path to market by eliminating the need for repeated verification testing. By front-loading process development, we ensure that design verification is a confirmation of quality, rather than a waiting for production transfer to identify and implement fundamental process changes.
This investment in early process development signifies a significant shift from traditional manufacturing timelines. By resolving potential production issues in the design phase, we minimize costly redesigns and avoid delays in later stages. This strategic foresight translates into a more efficient verification process, ensuring that when a product reaches design verification, it does so with a robust and well-defined manufacturing process already in place, setting the stage for a smoother transition into the market with a superior, reliable product.
Ready for Growth
As our clients evolve, so do their manufacturing needs. Our facilities and processes are engineered for scalability, ready to adapt to fluctuating production volumes while maintaining cost-effectiveness. This adaptability is essential for facilitating the growth and future-proofing the ambitions of our clients.
Intellectual Property: Our Pledge of Security
We recognize the invaluable nature of intellectual property, especially in Class III medical device innovation. Our robust IP protection and confidentiality protocols ensure that our clients’ proprietary advancements are securely guarded, providing a solid foundation for a trusted partnership.

The Vanguard of Technology and Expertise
Our investment in the newest technological advancements and ongoing staff development ensures that we remain at the cutting edge of Class III medical device manufacturing. This investment not only bolsters the quality of our products but also introduces cost-saving efficiencies, with our expertise serving as an invaluable asset to our clients.
Streamlined Supply Chain Excellence
Efficient supply chain management is indispensable for cost-effective manufacturing. We have honed a supply chain system that ensures the procurement of materials and components without compromising on quality or inflating costs, allowing us to deliver economical manufacturing solutions to our clients.
In conclusion, our strategic approach to the development and manufacturing of Class III complex catheters and implants is founded on the principle that exceptional quality and cost-efficiency can coexist harmoniously. Through meticulous planning, innovative manufacturing techniques, and an unwavering commitment to quality and client communication, we deliver services that meet the elevated standards of the medical device industry while also adhering to the financial realities of our clients. At Medical Murray, we don’t just manufacture medical devices; we cultivate partnerships based on shared goals of patient safety, quality, and value.
By Tanner Hargens