Design Verification
Design Verification (DV) consists of testing a medical device to collect objective evidence that the design outputs meet all of the predetermined design inputs and regulatory requirements. Ultimately, Design Verification provides assurance that the device is safe, functions as intended, and is ready for clinical use and/or regulatory submissions.
Design Verification support at Medical Murray commonly consists of the following:
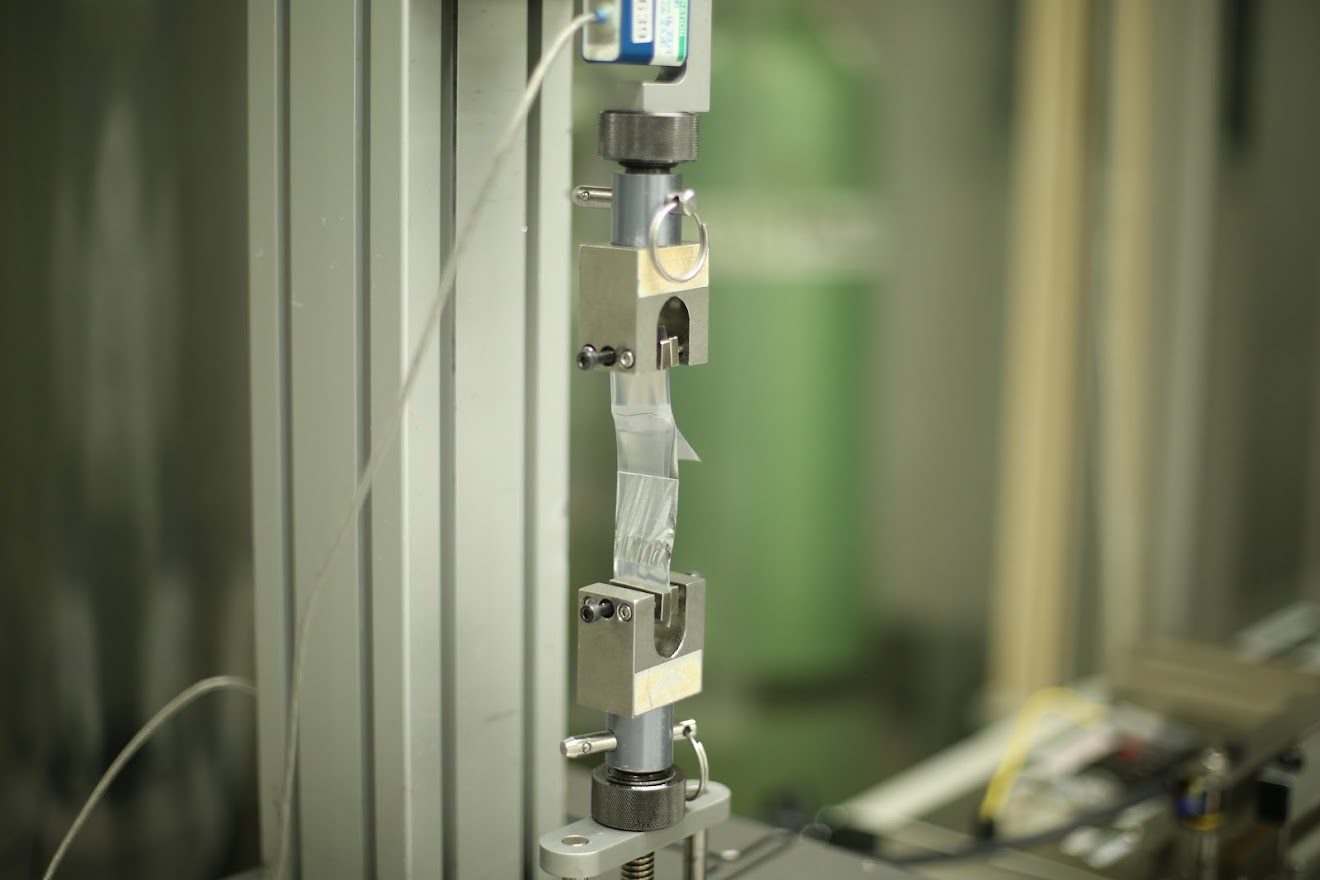
- Design FMEA
- Design Verification Protocols
- Device Master Record Documentation
- Process Validation Planning
- Packaging Validation and Report
- Bench Testing and Report(s)
- Cleanroom Assembly and Packaging
- Sterilization Validation (EO, Gamma, or eBeam)
- Ethylene Oxide Validation Adoption
- Biocompatibility Testing and Reports
- Shelf Life Validation (Accelerated & Real Time)
- Compiling Regulatory Submission Documents (IDE, 510k, PMA, CE Marking)
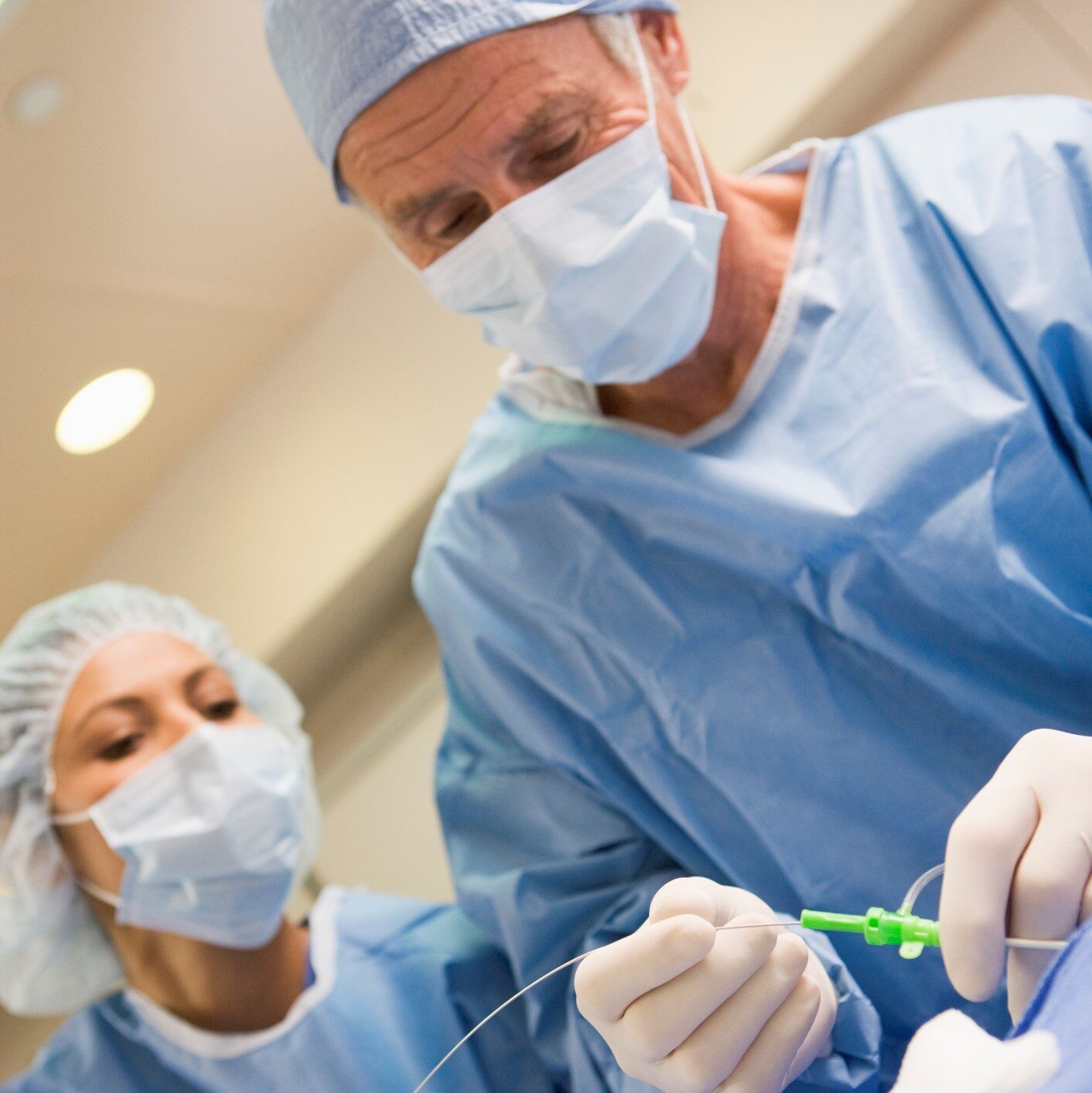
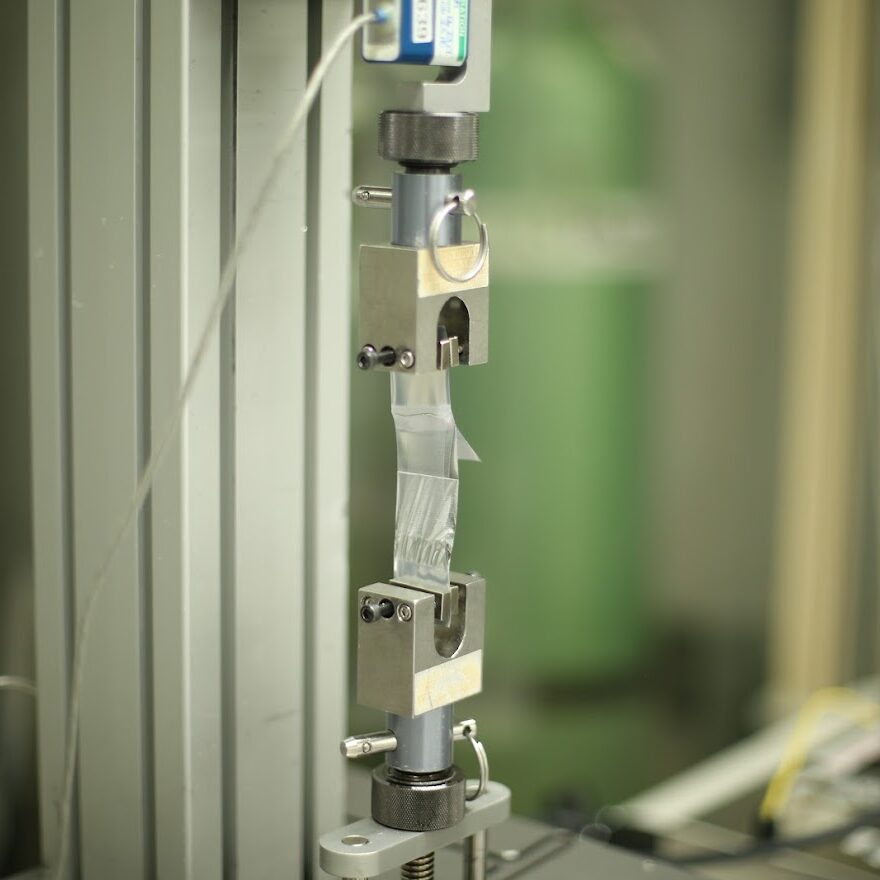
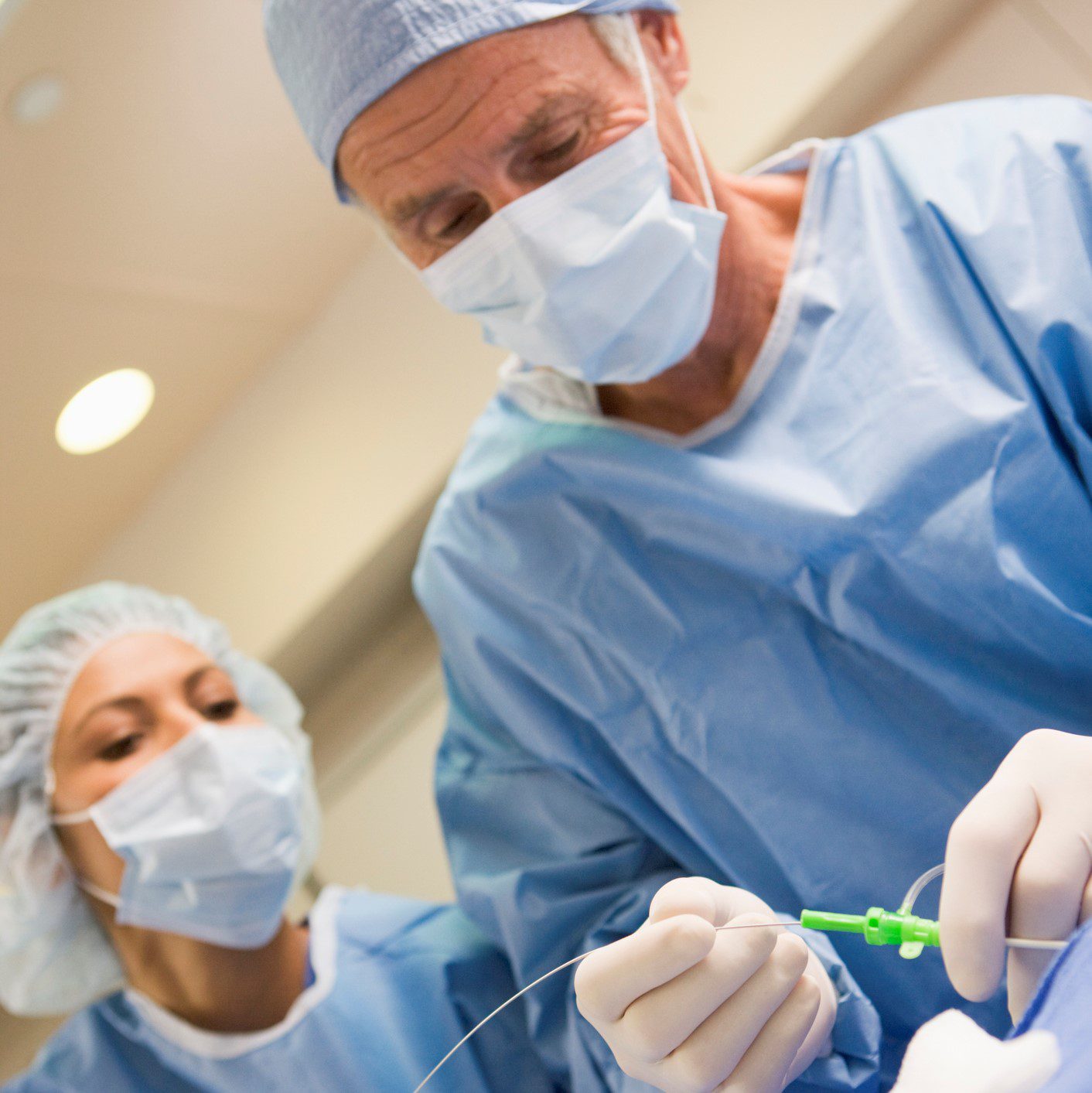
Design Validation
While Design Verification demonstrates that the medical device meets the engineering requirements, Design Validation demonstrates the device addresses the User Needs when put to use. According to the FDA, Design Validation is confirmation by examination and provision of objective evidence that the particular requirements for a specific use can be consistently fulfilled.
For the interventional products produced at Medical Murray, clinical evaluation is often necessary to validate the design. Design Validation support at Medical Murray commonly consists of the following:
- User Needs
- Labels & Instructions for Use
- Simulated Use Testing
- Animal Evaluation
- Pilot Production of Clinical Product