Injection molding intricate components for medical device implantables is a difficult task on its own. Add absorbable polymer to the equation and it becomes many times more challenging. This article reviews several of the barriers to success in this area of component fabrication for implantable medical devices.
By Tanner Hargens, Senior Biomedical Engineer at Medical Murray
Bioabsorbable implants often pose several advantages to their non-absorbable counterparts. Absorbable materials do not require a second surgical procedure to remove the device, often reducing total charges and the rate of infection. These polymers may be tailored to serve an initial purpose after being implanted and then transfer responsibilities to the natural tissue in sync with the healing process. Drugs can also be impregnated within the polymer matrix to release at a rate controlled by the degradation of the material.
Bioabsorbables are widely utilized for cardiovascular applications. Examples include ligation and closure of blood vessels along with absorbable drug-releasing stents and grafts. Many of these devices have small, complex, 3D structures and dynamic mechanical requirements (e.g., living hinges) that can only be formed by injection molding.
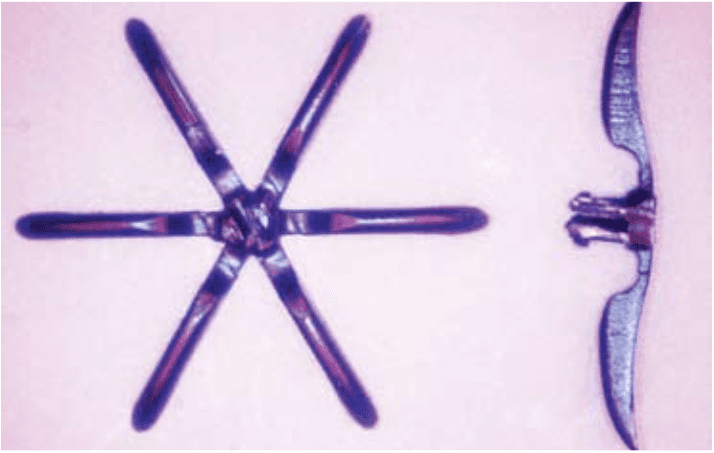
Injection molding first transitions a polymer from a solid-state to a semi-liquid state by heating the material above a threshold temperature. With a reduced viscosity upon turning into a liquid, the polymer can be injected (or forced) into the cavity of a mold. The process must then be reversed (i.e., the material must cool and return to a solid state)before it can be removed from the mold.
Bioabsorbable polymers can be injection molded with extremely small features and thin sections; however, this requires special equipment and consideration. The absorbable polymer should be processed at the lowest temperatures possible with the least amount of time exposed to the elevated temperatures. Each bioabsorbable will have a different temperature threshold that, when surpassed, will reverse the polymerization process resulting in monomer formation. Introducing an extra monomer into the material matrix can immediately change the mechanical properties, alter the degradation kinetics, and even make the material toxic. Conventional injection molding equipment and processes are unable to adequately perform such controlled and rapid thermal cycling.
In addition, presses need much higher injection speeds and pressures in addition, presses need much higher injection speeds and pressure to push melted polymer through tiny nozzles and flow channels. Higher injection speeds ensure the material will fill the part before it cools. Accurate screw and barrel design and injection control are essential. Molding very small parts generally are not recommended on machines larger than 20 tons because it is difficult to control such small shot sizes, and lab machines, though small, are not usually designed for precision control of volume production.

Bioabsorbable implants often pose several advantages to their non-absorbable counterparts. Absorbable materials do not require a second surgical procedure to remove the device, often reducing total charges and the rate of infection. These polymers may be tailored to serve an initial purpose after being implanted and then transfer responsibilities to the natural tissue in sync with the healing process. Drugs can also be impregnated within the polymer matrix to release at a rate controlled by the degradation of the material.
Bioabsorbables are widely utilized for cardiovascular applications. Examples include ligation and closure of blood vessels along with absorbable drug-releasing stents and grafts. Many of these devices have small, complex, 3D structures and dynamic mechanical requirements (e.g., living hinges) that can only be formed by injection molding.
For these reasons, specialized systems haveFor these reasons, specialized systems have been developed for injection molding small complex bioabsorbable parts. Medical Murray uses a molding machine called the Sesame, which was designed and patented (U.S. No. 6,267,580) by the company for creating small complex medical devices. The machine is designed to provide fast controlled injection and short material residence time. It uses a pneumatically driven vertical plunger for plasticating and injects with a tiny horizontal plunger (1.0 to 2.5 mm diameter) driven by a linear servo motor. Total injection time can be as short as 0.02 seconds. The Sesame’s features include very low melted volume and controlled high speed and high-pressure injection. This allows the molding of sub-micro size parts with complex geometric features from materials such as bioabsorbable polymers that would otherwise degrade in standard equipment. Parts have been produced on the Sesame measuring just 0.1 mm and weighing only 2.5 mg, or one-twentieth of a single pellet.
Tanner Hargens is a senior biomedical engineer and project leader for Medical Murray. He is responsible for medical device engineering research and development and specializes in implants, biomaterials, and minimally invasive procedures. Hargens also provides expertise related to commercializing medical products.