ePTFE, or expanded polytetrafluoroethylene, is a highly durable and biocompatible material that is often used in medical procedures where longevity, biocompatibility and controlled porosity is desired.

ePTFE is made from the same polymer as Teflon but expanded to create a porous structure. ePTFE can be processed with structural orientation to be very thin while maintaining high strength, integrity, and flexibility. This combination of traits makes ePTFE ideally suited for minimally invasive and implantable medical device designs.
Some of the most common uses of ePTFE in medical devices are stent and frame coveringsvascular grafts, heart valves, medical textiles (e.g. patches, Dural substitute, and surgical mesh), filters, and catheter shafts. There are some exciting, emerging technologies that use ePTFE for occlusion, flow diversion and other implants, as well.
ePTFE’s combination of strength and flexibility while having such a thin profile makes it an ideal choice for stent grafts. It is a highly durable material that can withstand the pressure of blood flow and be shaped to fit the specific contours of a patient’s blood vessels. ePTFE is also non-thrombogenic and biocompatible, meaning far lower risk of complications after placement.
Extruded ePTFE versus Electrospun ePTFE
Extruded ePTFE and electrospun ePTFE have different properties and characteristics that make them suitable for different applications. Extruded ePTFE is a highly uniform with a well-defined pore size and structure and is commonly used in devices that require high mechanical strength, durability and lower limit wall thickness. Extruded ePTFE can be subjected to post-processing steps to create extremely thin-walled extrusions or sheets. With specialized equipment and skilled operators, the wall thickness of extruded ePTFE can be reduced below 0.001” (25 microns), which can be advantageous for ePTFE implants delivered through a catheter.
Electrospinning ePTFE, on the other hand, produces a fibrous mesh with high surface area-to-volume ratio and a range of pore sizes, most is well suited for devices that require a higher level of porosity, such as tissue engineering scaffolds or wound dressings. Both extruded ePTFE and electrospun ePTFE can be used in vascular grafts, stent grafts or other implantable devices.
Properties of ePTFE
The properties of ePTFE vary depending on the medical device manufacturing process and the expanded ratio. When developing a medical device made of ePTFE, there are several specifications that should be considered depending on the targeted product requirements:
- Shape and Size
- Thickness
- Pore Size and Distribution
- Internodal Distance
- Volume Density
- Crystallinity
- Mechanical strength: sufficient to withstand implanted pressures and forces generated during implant loading and deployment
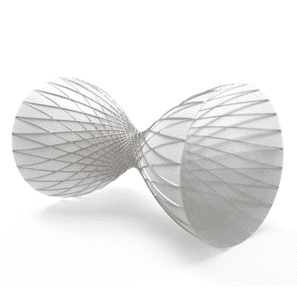
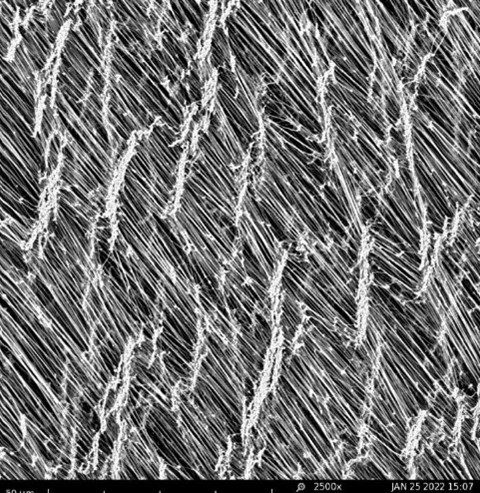
ePTFE is a versatile and useful material that can be used in a wide range of medical devices. Its strength, flexibility, and biocompatibility make it a great choice for applications that require these properties. Ultimately, the ePTFE properties will depend on the specific application and the trade-offs that are acceptable for each case.
There are a limited number of companies capable of processing ePTFE for medical device applications, so it is important to research and find a reputable and experienced manufacturer that can meet your specific needs.
Looking for a medical device manufacturing partner that specializes in ePTFE stent grafts? Contact us to learn more about how we can help you design and create the medical device you need.
By Tanner Hargens